In the decade since severe capacity constraints limited monoclonal antibody (MAb) production, the industry has adjusted, so that today, overcapacity is the issue, along with developing techniques to ensure product quality, reduce development timelines, and decrease costs, writes Ms Gail Dutton in a Genetic Engineering & Biotechnology News Feature Article on 15 February 2010. Many of these issues will be explored at IBC’s conference on ‘Antibody Development and Production’ in March 2010 as she points out.
Modern monoclonal antibody production - focus on quality by design, timelines, cost
Biosimilars/News
|
Posted 09/03/2010
0
Post your comment
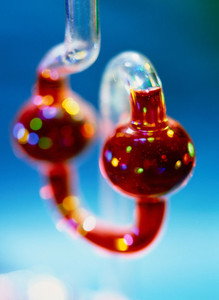
Ms Dutton writes that the FDA is also championing a Quality by Design (QbD) approach to drug production — even for biologics. Biogen Idec and a few other companies are participating in a QbD pilot programme with the FDA to develop a framework for applying that approach to biologics, according to Mr Vince Narbut, Director of quality technical systems at Biogen Idec Inc.
The QbD approach strives to establish a more thorough knowledge of the linkage between process parameters and the desired quality attributes of the product being produced. “Through a combination of quality risk management and more comprehensive scientific studies, it is possible to achieve greater process control and product quality/consistency,” Mr Narbut explained.
“By filing this information with the FDA it should, in concept, be possible to realize increased manufacturing flexibility, manifested by the ability to make process changes within the design space without additional regulatory approvals.” In contrast, the traditional approach requires a less developed understanding of the processes, but also provides less space for design modifications.
The trade-off, however, is that QbD requires more studies focused on quality attributes like structure–activity relationship and preclinical studies, formal risk assessments of each attribute, as well as more comprehensive evaluations of process parameters, raw materials, and their effect on the process/product. “This approach takes significantly longer when first starting, but once optimised, should take about the same time as the traditional development approach” Mr Narbut told.
Biogen Idec has used this product-development process for about two years. “It is implemented for one product developed in-house and is being incorporated into subsequent late-stage development processes. Our experience in the FDA pilot programme will be used to determine if we will pursue QbD regulatory filings in the future”. Based on some initial FDA feedback, it is clear that significantly more process-design detail and documentation will be required than is normally provided.
For companies considering adopting QbD for MAbs or other biologics, Mr Narbut advises them to start small. “Don’t plan a comprehensive QbD product-development effort without the internal resources and time to accommodate it”. As yet, “There are no detailed guidance documents and not much precedent. It may become more systematic if it catches on”, he said. (see also How to tackle overcapacity in monoclonal antibody production, Monoclonal antibodies modelling - predictive analytics and Improving monoclonal antibody production - antibody-drug conjugate technology)
Reference:
Gail Dutton. Trends in Monoclonal Antibody Production - With Capacity Issues Resolved, Firms Direct Attention to Quality, Timelines, and Cost. Genetic Engineering & Biotechnology News Vol. 30, No. 4. 2010 February 15.
Source: Genetic Engineering & Biotechnology News
Research
Reaching ESG goals in pharmaceutical development
What is the future for the US biosimilar interchangeability designation
General
Chinese biosimilars go global: growth, partnerships, and challenges
Stelara biosimilars enter US market with 85% discount in 2025
EMA recommend approval for aflibercept, ustekinumab, and pegfilgrastim biosimilars
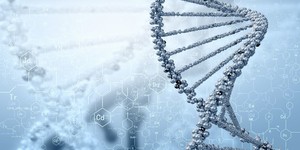
Biosimilars/News Posted 10/07/2025
The best selling biotechnology drugs of 2008: the next biosimilars targets
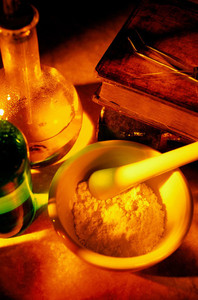
Post your comment