The US Food and Drug Administration (FDA) has released draft guidance on post-approval manufacturing changes for biological products, which outlines which changes have the least potential to affect product quality and how to document them in an annual report.
New FDA guidance on biological manufacturing changes
Home/Guidelines
|
Posted 25/08/2017
0
Post your comment
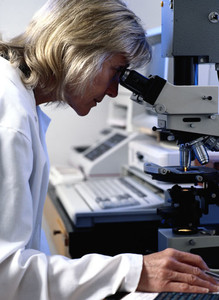
Changes to drug products after they have been approved must be submitted to FDA as minor, moderate or major. For the latter, applicants must submit a supplement and receive FDA approval before the product is distributed. For moderate cases, applicants must submit a supplement at least 30 days before distribution and, in some cases, the drug can be distributed as soon as FDA receives the supplement. For minor changes – which this new guidance relates to – applicants must notify FDA of the changes in an annual report but can still go ahead with production.
The guidance provides recommendations for Biologics License Applications (BLA) holders on changes that must be documented in an annual report, specifically relating to chemistry, manufacturing and controls (CMC) post-approval manufacturing changes that could have a negative effect on product quality.
FDA says any changes to the product, production process, quality controls, equipment, facilities or responsible personnel that occur after approval and that could have even the smallest chance of having an adverse effect on its quality must be documented in the annual report.
The annual report should list all the products changed and a statement that the effect of the changes has been assessed. It must also include a full description of all CMC changes, including the manufacturing sites involved, date the change was made, references to validation protocols and/or standard operating procedures and data from studies performed to assess the effect of the change on product quality.
The guidance, which was released following an increase in post-approval manufacturing supplements, provides several examples of CMC post-approval manufacturing changes that have ‘minimal potential’ to have an adverse effect on product quality, including the following changes:
Components and composition
– Elimination or reduction of an overage from the manufacturing batch formula previously used (to compensate for manufacturing losses).
Manufacturing sites
– A change to the site used for testing or labelling.
– A change in the manufacturing facility in an approved BLA that does not increase risk of contamination.
– A change in location of manufacturing steps within an area that is already listed in an approved BLA, in which the steps are part of a non-sterile drug production process and the new location does not affect contamination risk.
Manufacturing process, batch size and equipment
– Changes in mixing times for solution dosage forms.
– Reduction of open-handling steps, if there is a reduction in product exposure that improves product protection.
– For key sterile drug products, changes from a qualified sterilization chamber to another of the same design and operating principle (for containers/closures preparation when new chamber and load configurations are validated to operate within previously validated parameters).
Specifications
– Adding tests and acceptance criteria to specification for approved excipients.
– Change to a drug substance or product to comply with an official compendial test.
– Adding a test for packaging material.
– Tightening of acceptance criteria.
– Change in regulatory analytical procedure, if the acceptance criteria remain unchanged and the new method stays basically the same.
Container closure systems
– Change in the container closure system for storage of a non-sterile drug, as long as it does not increase risk of leachable substances and offers at least the same protection from air and moisture.
– Use of a contract manufacturing organization for washing of a drug product stopper.
The guidance thus clarifies the types of changes that can be documented in an annual report, rather than a supplement. It applies to all biological products listed in 21 CFR 601.2(a) but not blood-derived products, in vitro diagnostics, cellular and gene therapy products or vaccines.
Related articles
FDA user fee reauthorization bill passes US House of Representatives
Comments on switching in FDA’s interchangeability guidance from big pharma
Permission granted to reproduce for personal and non-commercial use only. All other reproduction, copy or reprinting of all or part of any ‘Content’ found on this website is strictly prohibited without the prior consent of the publisher. Contact the publisher to obtain permission before redistributing.
Copyright – Unless otherwise stated all contents of this website are © 2017 Pro Pharma Communications International. All Rights Reserved.
Source: US FDA
Policies & Legislation
ANVISA and Danish Medicines Agency renew health regulatory collaboration
Colombia and Brazil introduce reforms to enhance healthcare regulation
FDA issues guidance on AI use in drug and biologicals regulatory decision making

Home/Guidelines Posted 25/02/2025
The best selling biotechnology drugs of 2008: the next biosimilars targets
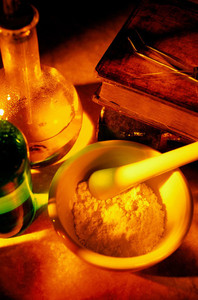
Post your comment